“Clean & Green” Machine Sets The Pace At Armstrong Coal Barge Facility
An electric-drive SENNEBOGEN 880 R-HD material handler helps coal producer meet all targets for cost-effective unloading operations
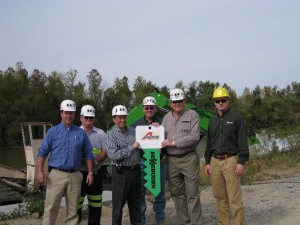
(from left to right) Matt Bueltel – Brandeis Machine Sales Rep, Ron Sharp – Armstrong Coal Equipment Manager, Gary Hirsch – Brandeis General Manager Crane & Material Handling, John Bruce – Armstrong Coal General Superintendent of Surface Mines, Kenny Allen – Armstrong Coal VP of Operations and Andreas Ernst – SENNEBOGEN Regional Sales & Marketing Manager.
Centertown, KY – In a few short years, Armstrong Coal has made great progress in its mission to supply clean coal for power generation. As its newest venture readied to start production, the Equality Mine on western Kentucky’s Green River, the coal producer set about commissioning a new dock facility 5 miles downstream to serve its coal preparation facility at Centertown, KY.
Now in full operation, the new Armstrong Dock has proved itself to be a showcase for clean, efficient productivity.
The centerpiece of the dock is one of the largest hydraulic material handlers in America: a 350,000 lb. SENNEBOGEN 880 R-HD. Swinging a 14-yard clamshell and designed to outpace much larger rope cranes, the 880 R-HD is a model of purpose-built efficiency. For a machine of its size, it’s also surprisingly quiet, economical and environmentally friendly, owing to the all-electric drive supplied by SENNEBOGEN.
Kenny Allen, Vice President of Operations at Armstrong Coal, is well acquainted with heavy equipment driven by high-voltage electric power instead of diesel. “We are already a major user of electric power, in around the 15 MW range. Our mines are using three electrically driven drag lines, with a fourth one set to go. We really chose the SENNEBOGEN machine for the way it’s built, but also because of its availability with electric drive.”
Green River goes green!
According to Gary Hirsch, General Manager of Crane and Material Handling for Brandeis Machinery, and its sister company Power Equipment, Brandeis recommended the SENNEBOGEN line to Allen. “Brandeis has a long-term relationship with the principal of Armstrong Coal and, with our experience in the construction and mining business that stretches over 100 years, we determined that SENNEBOGEN offered the ideal solution for their specific needs,” said Hirsch. Before purchasing the material handler, though, Allen took time to talk to other SENNEBOGEN owners in area. The tall green machines have become an increasingly common sight along the Ohio River, though most of the machines in these port facilities are smaller models in the SENNEBOGEN line. “It was all very positive,” Allen reports. “We could see how SENNEBOGEN has been taking the lion’s share of new facilities in the US. When we got looking at the specs of this machine, it impressed us.”
Allen explains that electric power is a cost-effective solution for his heavy excavation and material handling systems. And down on the river, he says, “there’s no concern about diesel fuel floating down the river, either!”
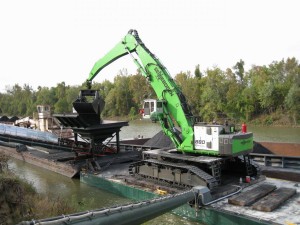
Unloading coal barges at rates up to 1800 tons/hr, the electric-drive SENNEBOGEN 880 outpaces larger rope cranes working on Ohio River ports.
Constantino Lannes, President of SENNEBOGEN LLC, has been a long-time proponent of electric-drive material handlers. “Our engineers began work on these units several years ago and they have had great success in different applications, from ports to recycling yards. Because of the way our factory is designed, SENNEBOGEN can deliver an electric-drive machine without the long delays that some customers have experienced elsewhere. Because of that, we’ve been able to get the jump on proving our equipment in the field.”
According to Lannes, low energy costs and “green” operations are just the beginning of the advantages of electric drive. By eliminating the diesel engine, most of the maintenance labor and parts costs are deducted from the machine’s operating budget. Depending on the energy costs, savings of 50% to 70% on operating costs are normal. Uptime is also improved with reduced service demands and no need for refueling – an important consideration for round-the-clock loading facilities.
River specialist at the helm
To build and operate the Armstrong Dock, Allen turned to Wabash Marine, a specialist in river construction and contracting based in Henderson, KY. “Wabash does everything for us on the water – and we take it from there,” says Allen.
Wabash mounted the material handler to a barge built to their specifications by Eagle Industries of St. Louis. Tom Moosbrugger, President at Wabash Marine, explains that components of the 880 R-HD were delivered one piece at a time by Brandeis, so the pieces could be staged for assembly on the barge. Before assembly began, Wabash constructed a platform of 1-ft. oak beams and made provisions to lash the machine to the platform. Completed, the barge was brought to the Armstrong Dock, 100 river miles upstream.
“It works like a dream!” says Moosbrugger. “This is the first hydraulic crane I’ve worked with. We did a rope crane with an 18 yard bucket. That was a 1000 tons/hour machine; and this one now is going 1700 to 1800 tons/hour. It’ll go as fast as we want it to go.”
Wabash continues to work on the Armstrong Dock maintaining the equipment and operating the material handler. “We’re still learning as we go,” Moosbrugger admits. “We reinforced some of the mooring attachments, just because of the strength of the machine and the rocking motion of the barge.”
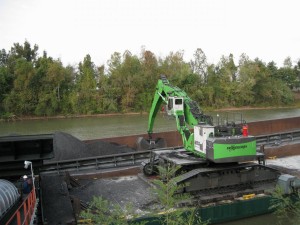
Weighing in at 350,000 lbs., the SENNEBOGEN 880 was lashed to 1-ft. oak beams on a custom-built barge, then floated 100 miles upstream to the Armstrong dock facility.
Simple, but effective
For the Wabash operators who are moving coal for Armstrong everyday, the learning curve was very quick. “SENNEBOGEN and Brandeis arranged training for us,” says Moosbrugger, “but there really wasn’t much training needed. Our guys are experienced crane operators, and this is a very simple machine to run. It’s very smooth. And they like how they can elevate the cab up and out to get over the barge and look right down into it.”
Armstrong Coal’s 880 R-HD features SENNEBOGEN’s popular hydraulically elevating cab. The operator can move the cab up and out, within a radius of almost 20 feet. This allows him to achieve the best vantage point for seeing the target area while loading as well as the area around the machine.
According to Brandeis’ Hirsch, the cab can also be ordered with a floor-level window to improve downward visibility. As well as helping the operator work more productively, this cab configuration can be a valuable safety feature, continued Hirsch. “When unloading barges, for example, the machine operator can maintain a clear line of sight to a skid steer performing clean-up work inside the barge.”
With the new mine, the dock facility and the coal preparation plant all operating smoothly, Kenny Allen looks forward to a growing future. “As the demand increases for clean coal, we’re prepared to move up to 4.5 million long tons through here annually. This facility is equipped to deliver coal matched to the fuel requirements of our customers’ generating systems, and we can deliver it by barge, by rail or by truck.”
About SENNEBOGEN
SENNEBOGEN has been a leading name in the global material handling industry for over 65 years. Based in Stanley, North Carolina, within the greater Charlotte region, SENNEBOGEN LLC offers a complete range of purpose-built machines to suit virtually any material handling application. Established in America in the year 2000, SENNEBOGEN LLC has quickly become a leading provider of specialized equipment solutions for recycling and scrap metal yards, demolition, barge and port operations, log-handling, transfer stations, waste facilities and the tree care industry from coast to coast. A growing network of distributors supports SENNEBOGEN LLC sales and service across the Americas, ensuring the highest standard of professional machine support and parts availability.
For more information on the full line of SENNEBOGEN green line material handlers, contact:
SENNEBOGEN LLC
1957 Sennebogen Trail
Stanley, NC 28164
Tel: (704) 347-4910 or fax (704) 347-8894
E-mail: sales@sennebogenllc.com