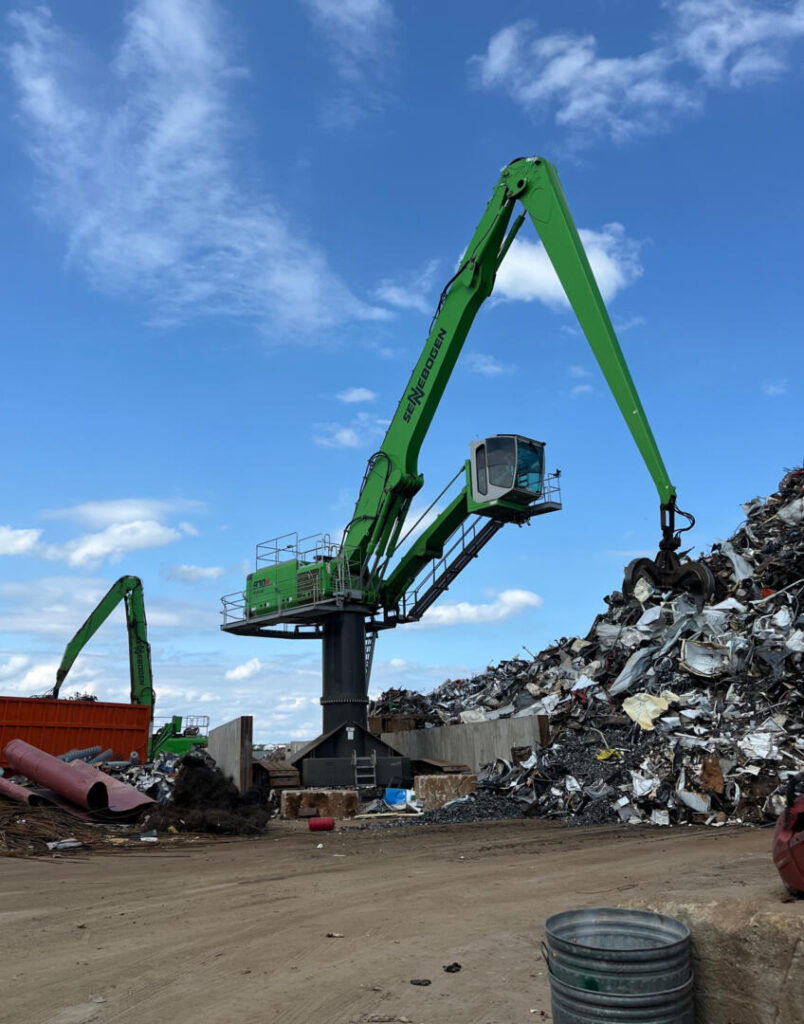
A unique power-supply arrangement allows Cimco’s electric-drive 870 to pick from multiple stockpiles on both sides of the shredder’s infeed.
Sterling, IL – Ron Brenny is Operations Manager for the largest of seven scrap recycling yards owned by Cimco Resources in Illinois and Wisconsin. The 26-acre facility in Sterling, IL, can receive as much as 800 tons of material a day, from plastics to electronic waste, but the bulk of it is destined for the site’s Metso mega-shredder. Cars and farm equipment, demolition scrap and industrial metals are meticulously sorted to match orders for shred from nearby mills.
As Brenny says, “We’re pretty full most of the time. We’re using our whole 26 acres. I have a lot of piles!” But with the arrival of Sterling’s new SENNEBOGEN electric-drive 870 Hybrid material handler this summer, the entire landscape of Brenny’s yard is changing.
Reaching for a simpler process
Cimco’s current fleet of 17 SENNEBOGEN scrap handlers is comprised of the mid-range units typical for scrapyard applications: 830 and 835 models weighing in at 85,000 to 120,000 lbs. (38,500 – 54,500 kg). In comparison, the new 870 Hybrid is a monster: over 220,000 lbs. (100,000 kg).
“Our main objective was to get the reach,” Brenny explains. Mounted on a 9-ft pedestal with a tracked undercarriage, the 870’s 90-ft boom can reach multiple piles of sorted material without maneuvering. It’s this extended working radius that has changed Sterling’s material handling and stockpiling processes.
Until now, trucks were offloaded at the far side of the yard. To feed the shredder, required material was loaded into trailers and moved up to the shredder’s infeed area, where it was offloaded into piles again. One of the 830 or 835 machines could then move it onto the infeed belt. Now, with the 870, several steps are removed from the flow of material through the yard.
“So that was our goal: instead of transloading everything up to the infeed, we can simply unload right there at the infeed and just grab what we need when we want to run it.” The new setup is efficient for equipment and for manpower, he says, and it greatly simplifies scheduling the movement of material and really simplifies his life.
With the 870 in service, not only can they position more stockpiles close to the infeed, but it can also pile more material. “We’re actually able to increase our yard space because we can pile higher,” says Brenny. “That means we’re using less ground, so we’re opening up more yard now.” Seeing the impact the 870 has made, Brenny now looks forward to bringing in a second 870 to service the north end of the yard, adding further to Sterling’s total capacity.
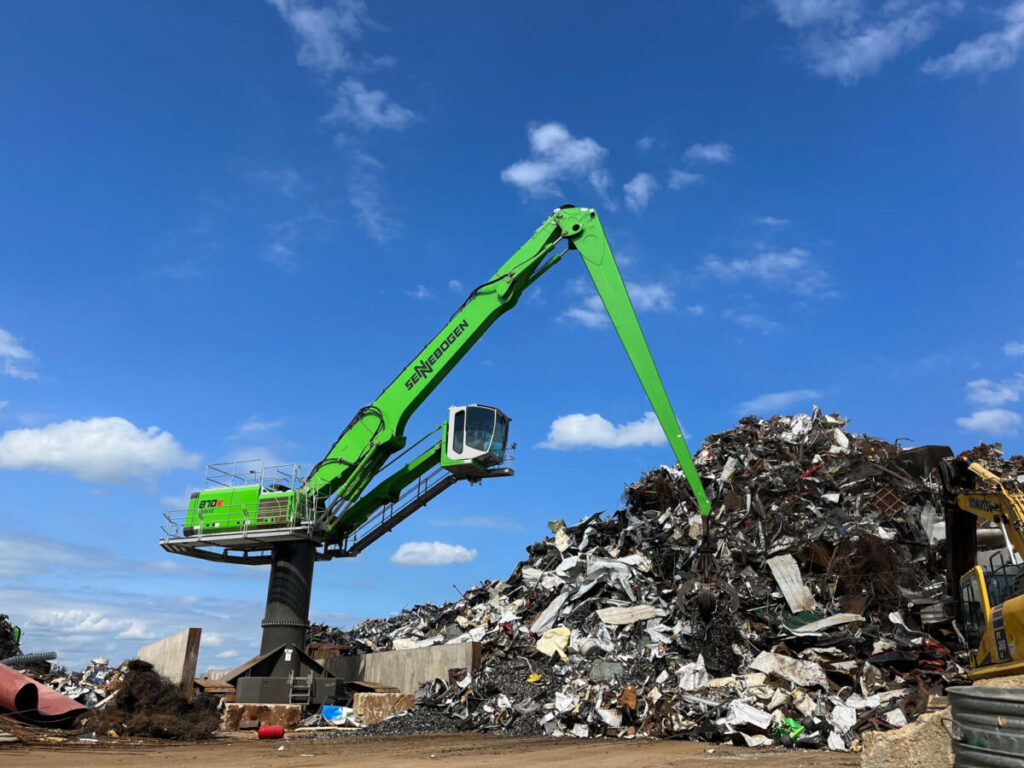
The long reach and fast cycle times of the SENNEBOGEN 870 Hybrid allowed Cimco’s Sterling facility to streamline logistics throughout its 26 acre yard.
Long reach, fast cycles
When Cimco first decided to look into upsizing its shredder loading equipment, the Sterling team was open to all options. Initially, Brenny and his Yard Superintendent, Mike Kapple, and Cimco CEO John Gralewski were attracted to a new, competitive tower crane. However, a video demonstration of the 870 changed their minds. “They were just showing the machines at work side by side, loading a barge. And I started counting. And I could see how many cycles the 870 made compared to the other crane. And I’m like, well, that’s a no brainer, guys! That tower crane won’t be able to keep up with my shredder!”
According to Brenny, his operators felt the same way when the 870 was finally onsite. “They’ve been feeding the shredder with an 835 for 15 years; they know the cycle times. We were all impressed with how fast it is for a big machine, with so much stick out there. They got up in there and were amazed how fast it goes. It’s been in operation since July and they’re still ecstatic with it.”
Less cost, more uptime
While the Sterling yard is now handling material more efficiently, Brenny is also seeing direct savings in operational costs with his newest SENNEBOGEN. The 870 Hybrid features SENNEBOGEN’s distinctive Green Hybrid energy recovery system. Its simple hydraulic design uses the weight of the boom to capture hydraulic pressure on each downstroke, then releases the pressure on the next upstroke to assist the lift. As a result, Green Hybrid models save up to 30% of the machine’s operating cost for energy.
Brenny admits that the company made a significant investment in infrastructure to deliver the necessary power to the 870’s location at the infeed, but he has no regrets. “That money up front, we’re getting that back every day,” he reports, “just by not pulling up to the diesel barrel every day. And we have no downtime for refueling either. The operator just gets in it, hits the button and he’s ready to go all day.”
“With the electric, I can say it’s just a big super bonus for the maintenance side. It’s quiet. There are so many more issues involved with a diesel engine; you got DEF and oil changes and everything else, you know. And that’s all gone!”
Dependable machines and service
Uptime and dependability were key factors for Cimco when the firm began renewing its fleet in recent years. The Sterling site acquired new machines from another OEM, but soon decided to switch back to SENNEBOGEN. “I guess, mainly, it was just the dependability. We just had so many issues with them trying to keep them running; a lot of problems, whether it was the engine or the hydraulic system. We’re all SENNEBOGEN now. That was a good move on our part.”
Brenny also credits the SENNEBOGEN distributor in his area, Alta Equipment, for their role in keeping his scrap handlers on the job. “We try to do most servicing ourselves,” he says, “but when it gets into stuff a little over our heads, we can talk to them, and they help us out over the phone or sometimes come out and get the answers and we’re going again. The whole organization is good to work with: the salesman and the mechanics, they’re good. And they have the parts that you need when you need them. That’s pretty impressive. If we say overnight, we get it the next day.”