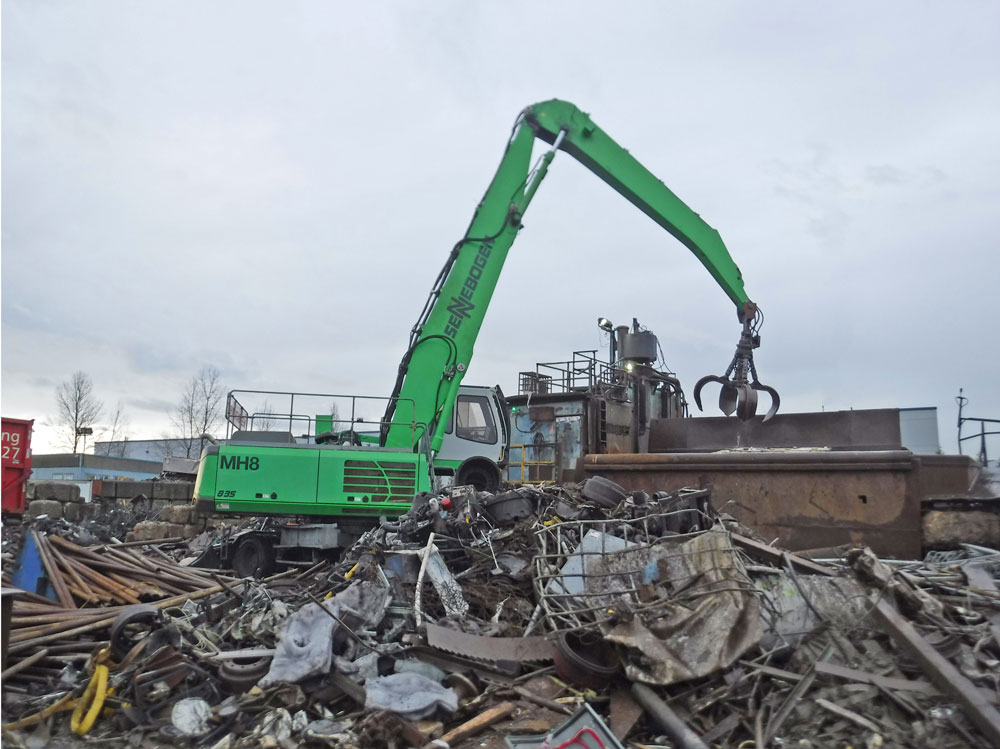
Even with the cab only partially raised, the operator has a bird’s eye view of the inside of the baler.
Burnaby, BC – “It’s difficult to find heavy equipment mechanics, generally,” says John Anderson, of ABC Recycling. “If we don’t have the people we need on our own payroll, we can end up waiting a long time for machine service. Having our own team of factory trained technicians makes a huge difference.”
Anderson is ABC’s Director of Maintenance in British Columbia. His goal of self-sufficiency is one reason ABC has been growing its fleet of SENNEBOGEN material handlers over the past 10 years. His SENNEBOGEN Sales Representative, Logan Strohm, of Great West Equipment, is sympathetic to the cause. “We have 11 service branches here in BC, but that still leaves our techs with a lot of territory to cover,” he admits. “That’s why we recommend that customers take advantage of the free factory training that SENNEBOGEN offers.”
With 8 recycling yards under the ABC Recycling flag in BC and one in Alberta, the firm has been operating in the region since 1912. A service crew in Burnaby supports the SENNEBOGEN machines there and in nearby Surrey. The fleet includes SENNEBOGEN 835 M and 830 M models, equipped with both grapples and magnets. “We’ve had very good success with these machines,” Anderson reports. “The 835 seems to be the right machine for everything we do: whether feeding stationary shears and balers, or loading trucks and rail cars.”
Free factory training
Anderson’s maintenance staff as well as operators have attended the SENNEBOGEN Training Center in Stanley NC. The Training Center, part of the 100,000 sq.ft. head office complex built by SENNEBOGEN LLC, provides classroom instruction as well as hands-on training with a demonstration module and full-size machines in a 3-storey high indoor bay. The Level I course and the Level II advanced program for technicians are 5-day programs offered free to dealers and their customers.
“It’s a very impressive facility,” says Anderson. “And while you’re there, you also get to see the extent of their parts inventory. As well as regular and routine service items, they also have a huge inventory of major components on hand such as pumps, engines, cylinders, axles and even boom and stick assemblies. You can see the company has invested heavily in parts for North America.”
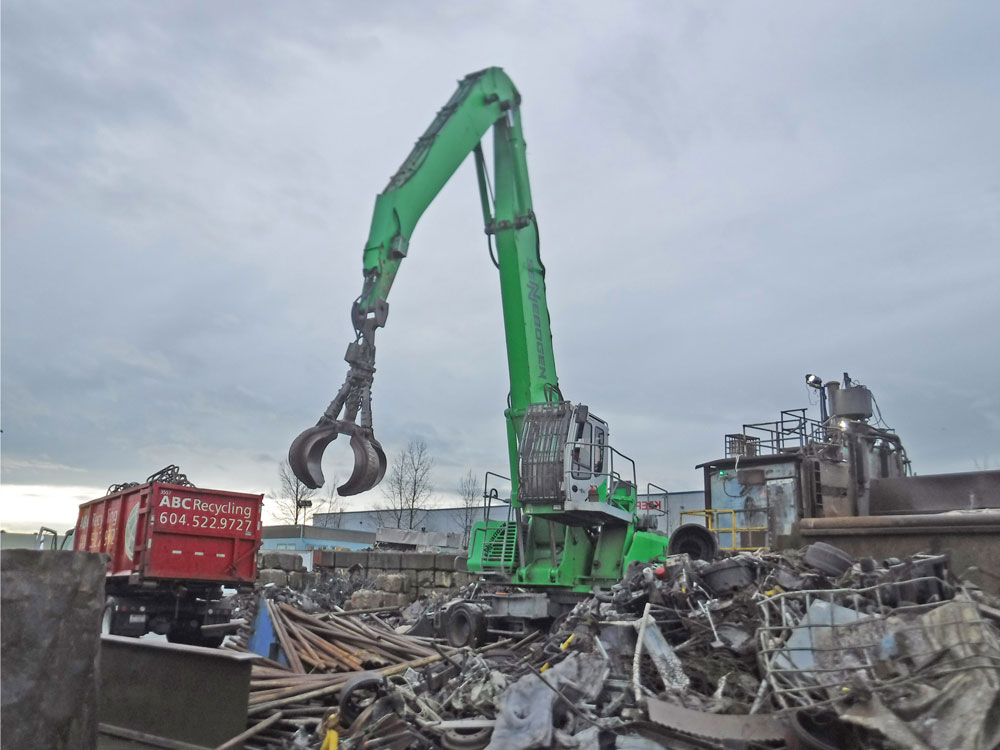
The combination of the reach and the view allows the operator to set up “his office” to his advantage for maximum productivity.
The choice of operators and technicians
ABC technicians and operators also take an active role in ABC’s purchase process for new equipment. According to Anderson, the maintenance team appreciates how SENNEBOGEN simplifies access to routine service points. The layout of maintenance components has been well designed, with most service and diagnostic items accessible from ground level. Hydraulic diagnostic ports are easy to reach, electrical fuses and relays are all arranged together in the main panel, accessed on one side of the machine from ground level. Auto-lubrication is standard equipment on SENNEBOGEN machines, which further simplifies maintenance tasks and extends the life of major components.
Anderson listens to his operators’ recommendations as well. “They are in the machine eight hours a day. We want to be sure they have a comfortable operating environment along with good functionality. They like the SENNEBOGEN Maxcab for its visibility and its two-camera system. They tell us the seating is comfortable and the machine is easy to handle.”
Ready access to low cost parts
The parts warehouse also attracted ABC to SENNEBOGEN machines. Anderson notes that, where many machines are designed with proprietary components, SENNEBOGEN uses commonly available parts wherever possible for power, hydraulics, electrical and other service requirements. This approach advances Anderson’s goal of self-sufficiency. “We can get all the parts we need from our dealer, of course, but we can also source parts locally. With their Cummins engines, we can find routine parts almost anywhere. Some parts might be a challenge for us to bring across the US border, but our dealers (Great West in BC and Strongco in Alberta) are able to help with expediting that too.”
In the long run, the simplicity and serviceability of the SENNEBOGEN machines lead to a lower lifecycle cost for ABC. “We do track all that detail here,” Anderson says. “Run time, fuel, maintenance labour and spare parts, all go towards our total cost of ownership analysis. Using industry standard components and Cummins service parts saves money for us. With our own crews and easy parts supply, the SENNEBOGEN equipment needs little downtime for service and repairs, so that brings down our total operating cost.”